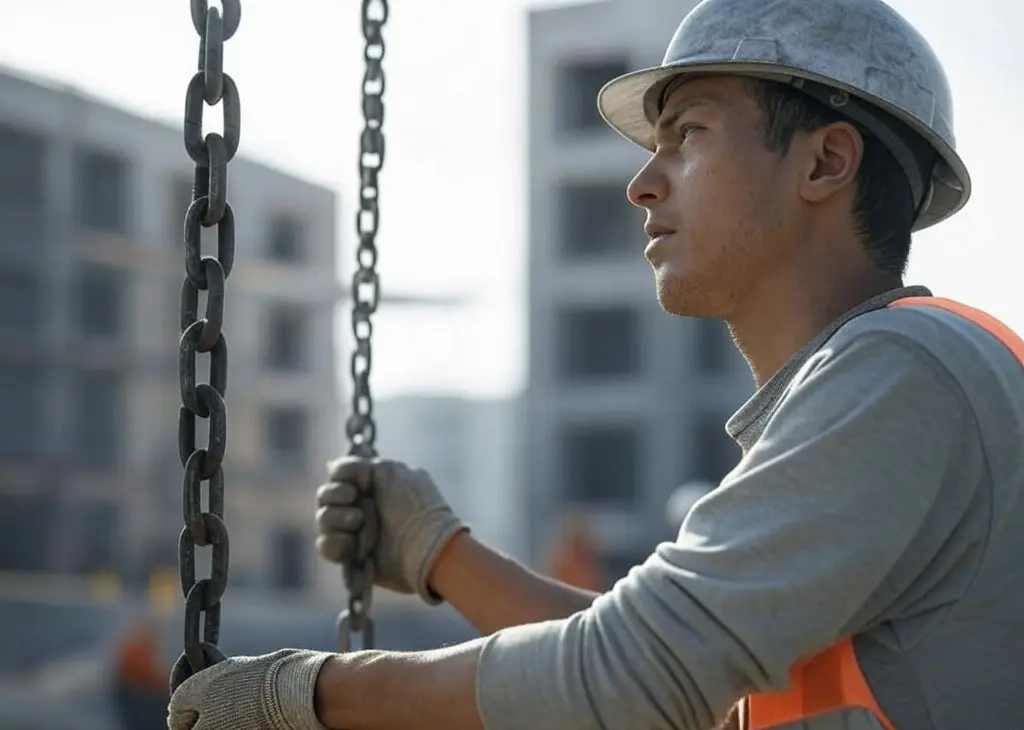
Construction crews involved in real estate development have to inspect all site and hoisting equipment—chains, hooks, pulleys, and other key components—periodically. Identification of faults at an early stage, including elongated chains, cracks, and rust, prevents costly safety risks and delayed timelines.
That’s why regular inspections and smart maintenance are key to maximizing the lifespan and performance of lifting chain and components. Equipment failures can disrupt progress and pose serious risks.
Here’s how to keep your lifting chains and other vital tools in top shape for a successful project.
Inspect Chains Regularly for Wear and Damage
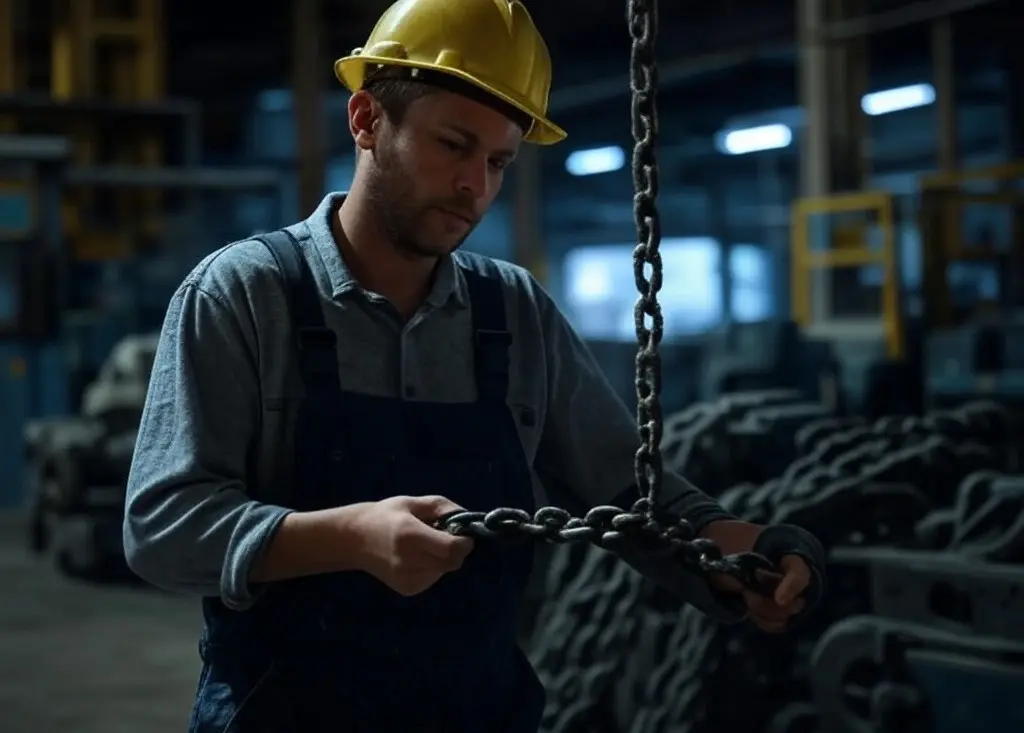
Before starting work, inspect the chains and critical items such as pulleys, hooks, and attachments for rust, cracks, and elongated links, or worn sections that could weaken the chain’s strength. Identifying them early keeps operations moving and saves you money on maintenance.
For bigger projects, you should schedule regular professional inspections. Experts can catch hidden defects and make sure your equipment meets all safety standards.
Keep Chains Clean and Lubricated
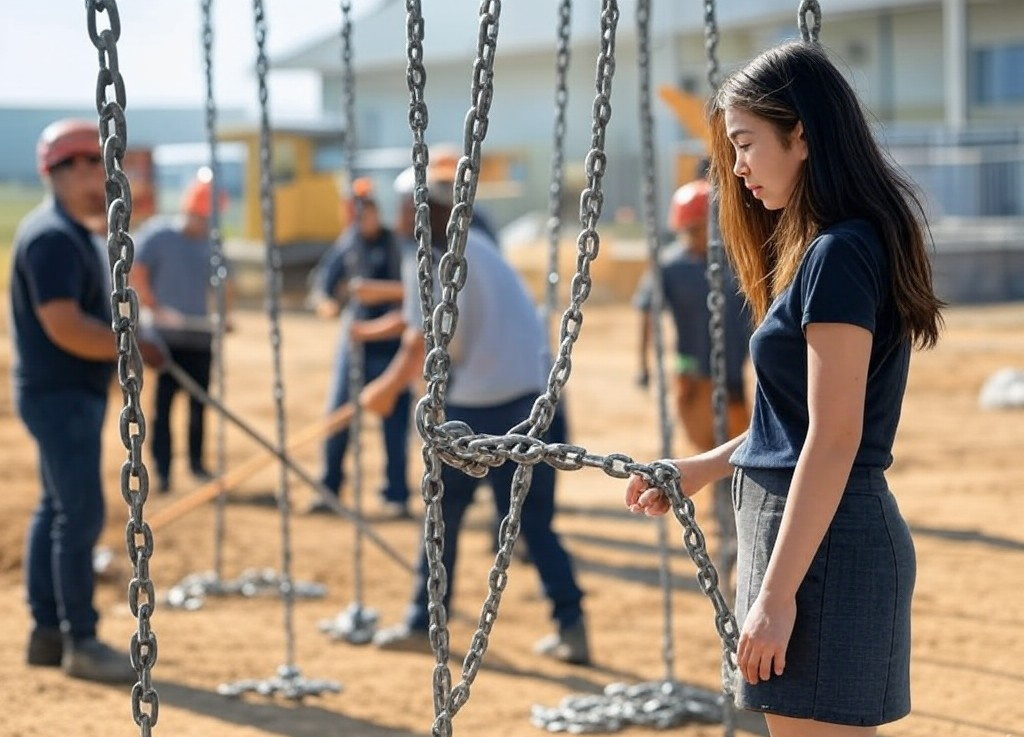
Construction areas are dirty, and that can cause your clothes or gear to wear out quickly due to dirt, moisture, and grime. It’s important to keep your chains clean. Otherwise, even simple tasks like unpacking loads can become a struggle if things get stuck for too long.
And don’t skip the lube! A good chain lubricant cuts down friction, fights rust, and keeps your chains working smoothly under heavy loads. Treat your equipment right, and it’ll keep the job moving without a hitch.
Invest in High-Quality Equipment
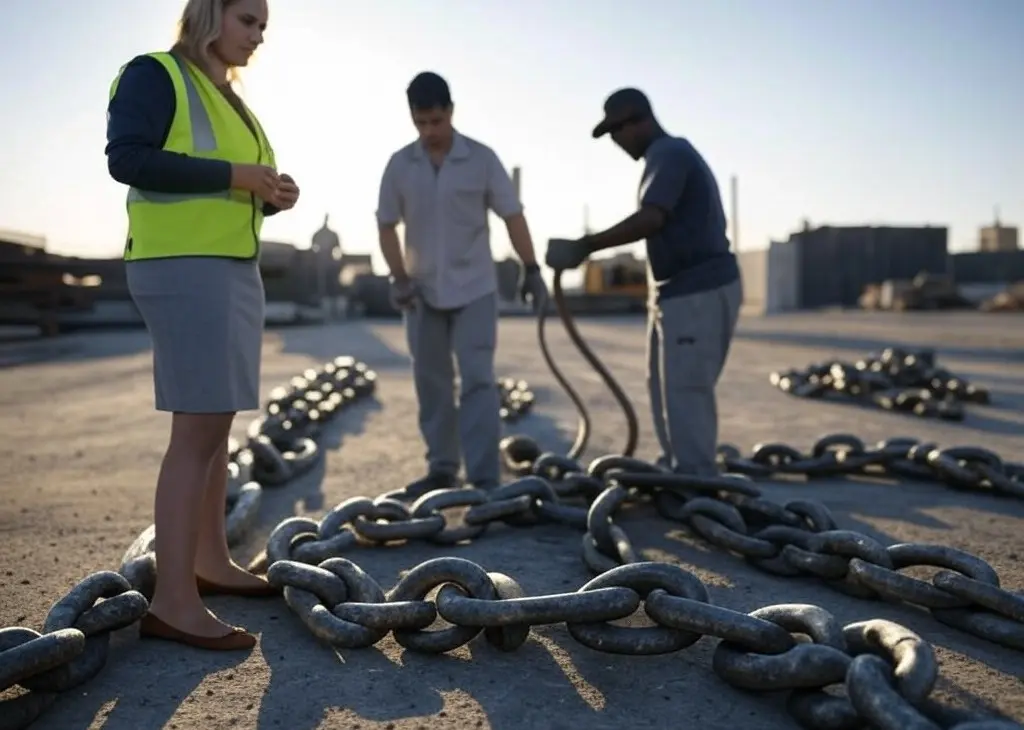
High-quality lifting chains and spares cannot be a luxury, but a necessity, in real estate development. Any form of failure in such items cannot be borne, and such failure can cause loss of time at a critical stage in development work.
Trusted suppliers provide durable chains and accessories built to withstand demanding conditions, ensuring that your operations stay efficient and safe. While it might cost a bit more upfront, investing in quality pays off in reliability and peace of mind.
Follow Load Limits and Usage Guidelines
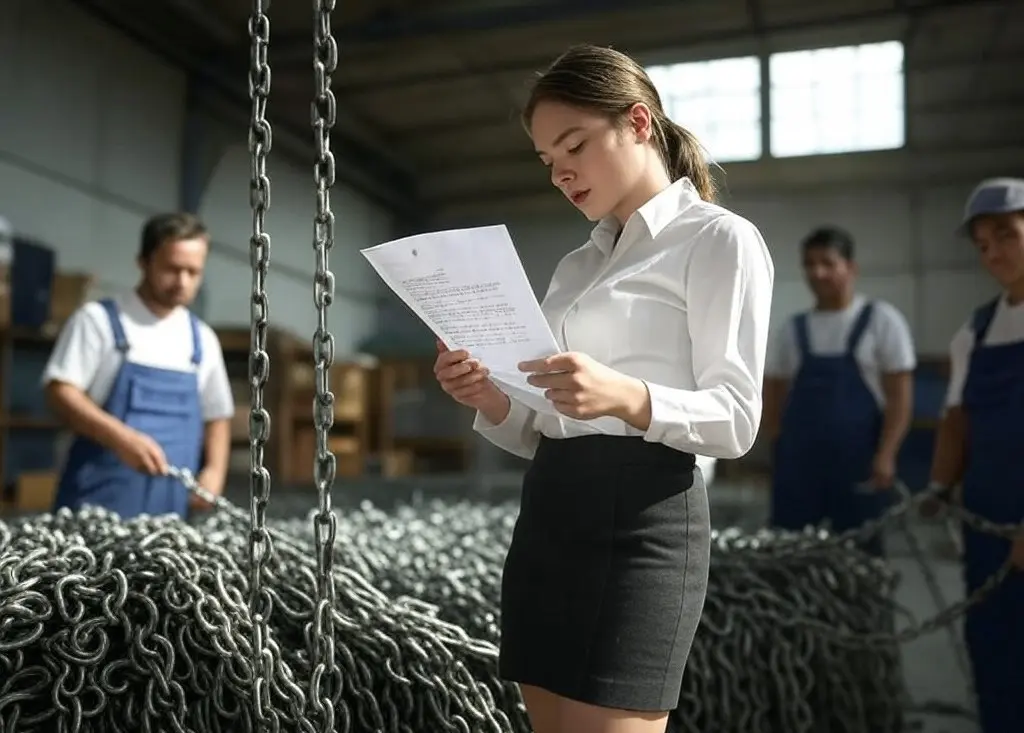
It is important that every member of your team knows that lifting chains have a Working Load Limit (WLL). This is because if you exceed the maximum weight that it can safely handle then this will be very dangerous. To avoid equipment damage and injuries, ensure that your crew comprehends and adheres to these boundaries.
Also, avoid risky practices like shock loading (sudden jerks) or twisting chains. Lifting chains are designed for straight pulls under steady tension—anything else can weaken them over time and increase the chance of breakage.
Store Chains Properly When Not in Use
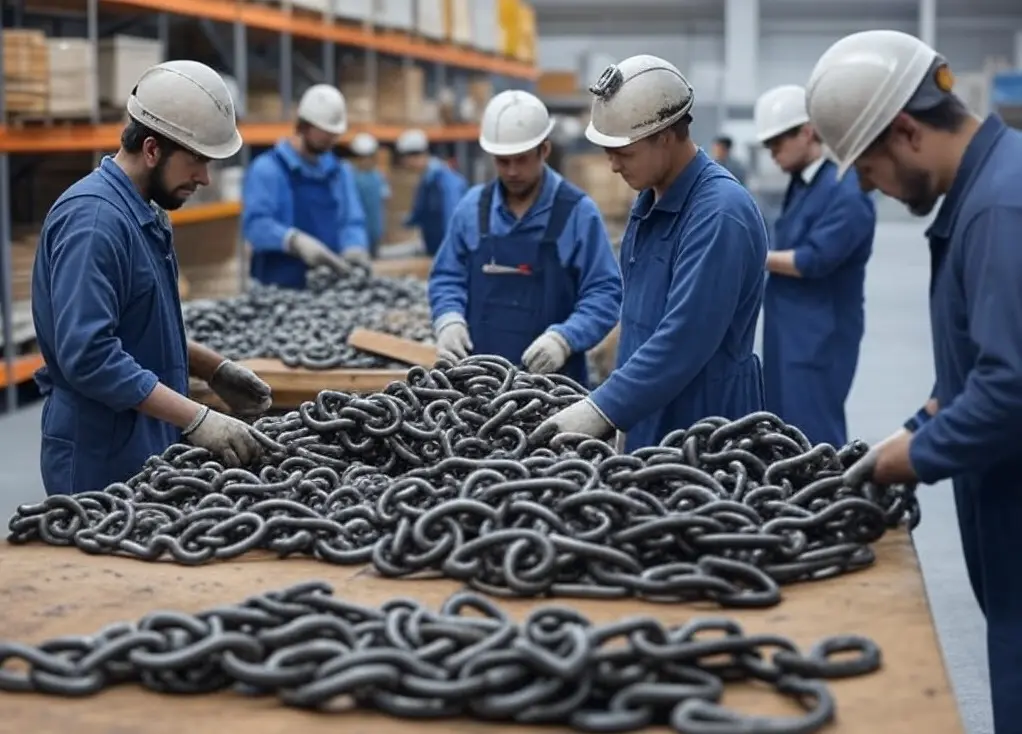
When your lifting chains aren’t in use, proper storage helps protect them from damage. Keep them in a clean, dry place, away from moisture and extreme temperatures. Hanging chains on racks prevents tangling and deformation.
Exposure to direct sunlight can also weaken metal over time, so store chains in a shaded area. Taking these precautions will keep your equipment ready to go when you need it.
Schedule Professional Inspections and Repairs
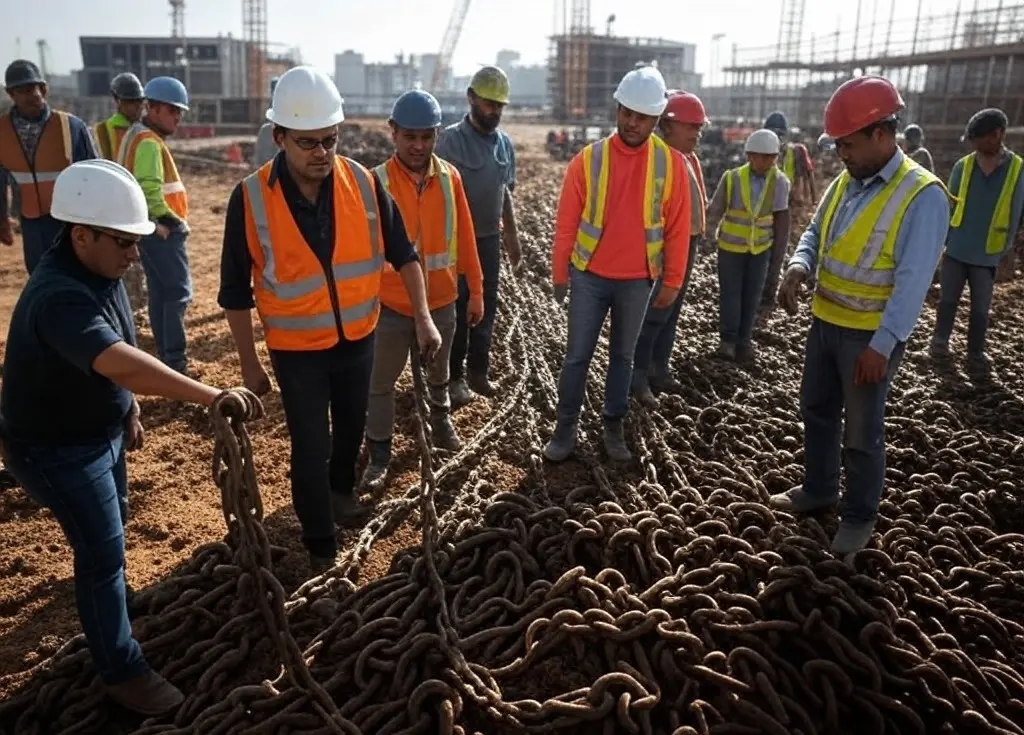
While routine checks are essential, professional inspections provide an added layer of safety. Experts can detect hidden issues and ensure that your lifting chains meet local construction regulations.
If a chain shows serious wear or damage, replace it immediately. Using faulty equipment can lead to dangerous failures, putting both your crew and the project timeline at risk. Don’t take that chance—be proactive with repairs and replacements.
Final Thoughts
For any construction project to be successful, there is a need for the right kind of equipment. As long as you manage to keep up with maintaining, inspecting, and following good safety rules of practice on a regular basis, then you will be able to prevent any interruption that may be very expensive, as well as take care of your employees.
Invest in your equipment, stick to the plan, and build with confidence!