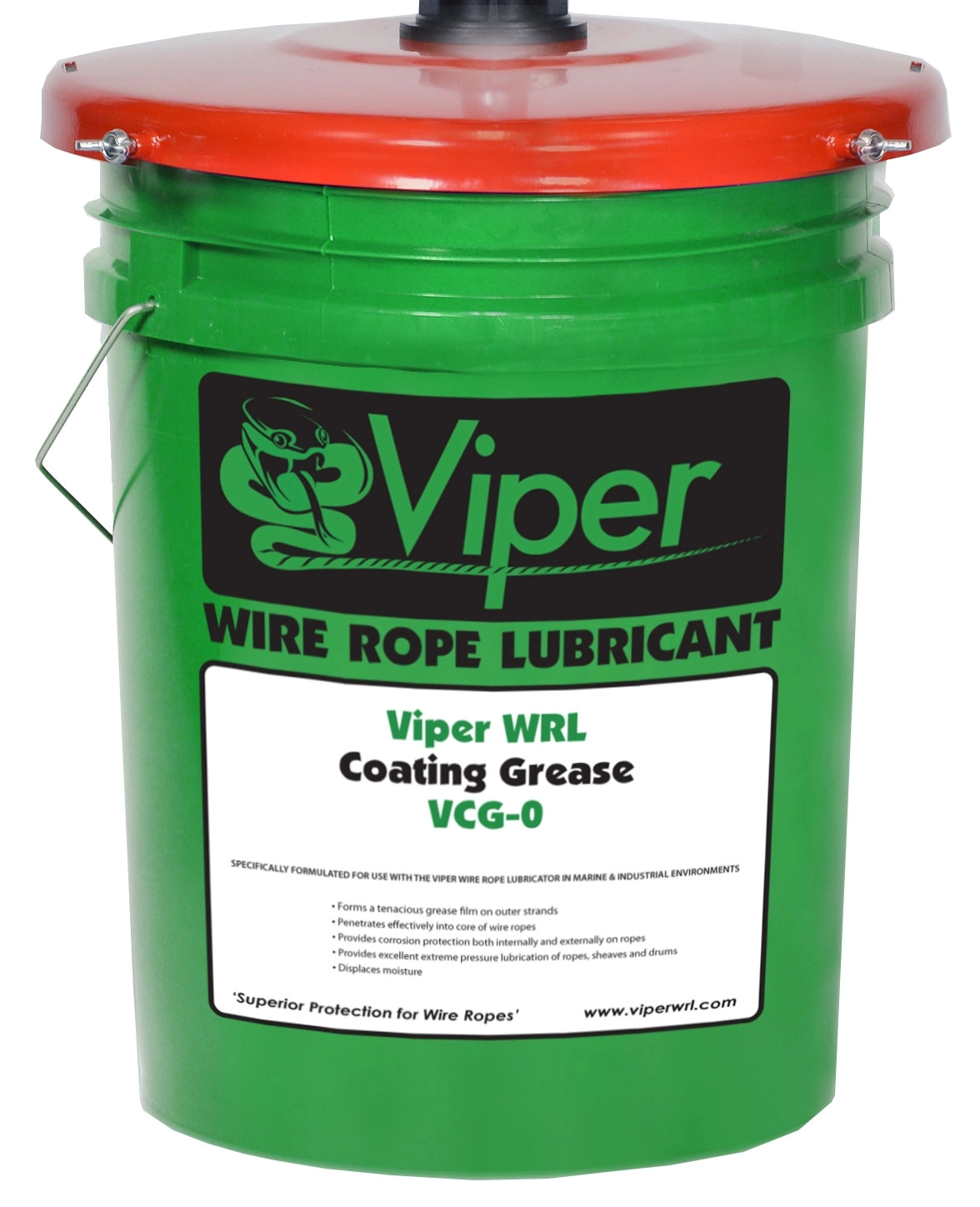
Wire ropes are used in many heavy-duty machines and equipment. From elevators to cranes to mining shafts, wire ropes take on tough tasks, lifting and moving heavy loads. According to experts like Viper WRL, wire ropes need special care and maintenance to work properly and safely. An important part of that care is keeping them lubricated. This article will explain what wire rope lubricant is and why it matters.
What is a Wire Rope?
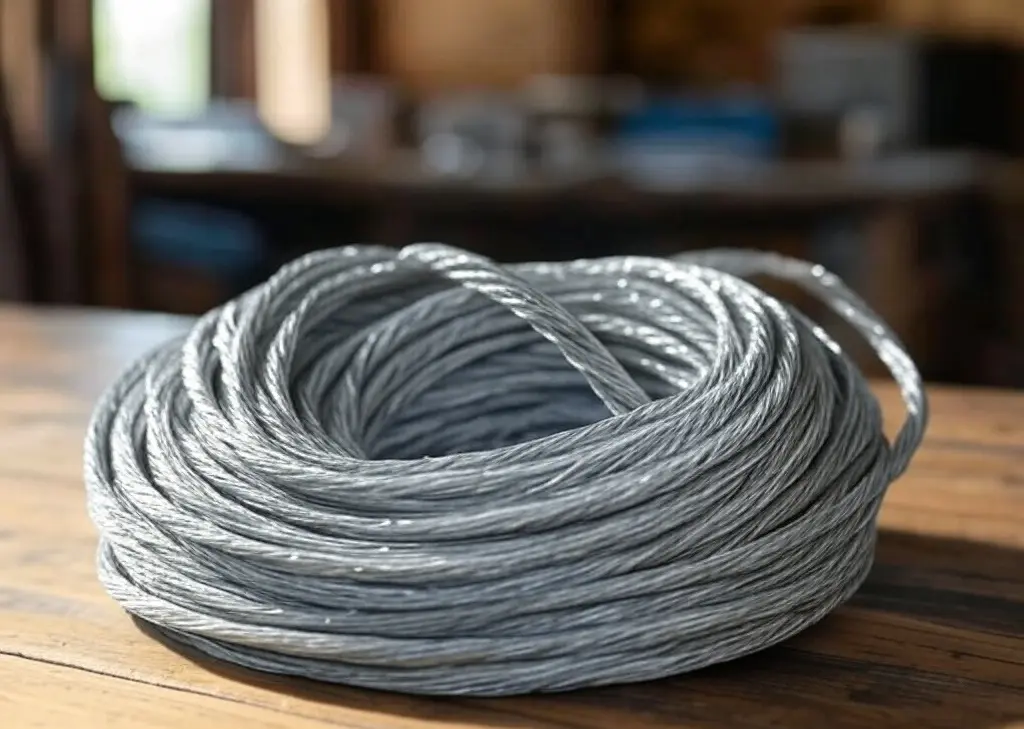
Wire ropes are constructed consisting of a number of small wires that are then twisted together to form larger strings. The strands are then strung together to create the complete rope.
The most commonly used metal in the production of wires is steel. Wire ropes come in various dimensions and strengths, allowing them to carry different weights. They range from very thin ropes to robust and heavy-duty ones.
Wire ropes are popular because they are very strong yet pliable. They are ideal for pulling, lifting, and supporting a variety of equipment and items
Why Lubricate a Wire Rope?
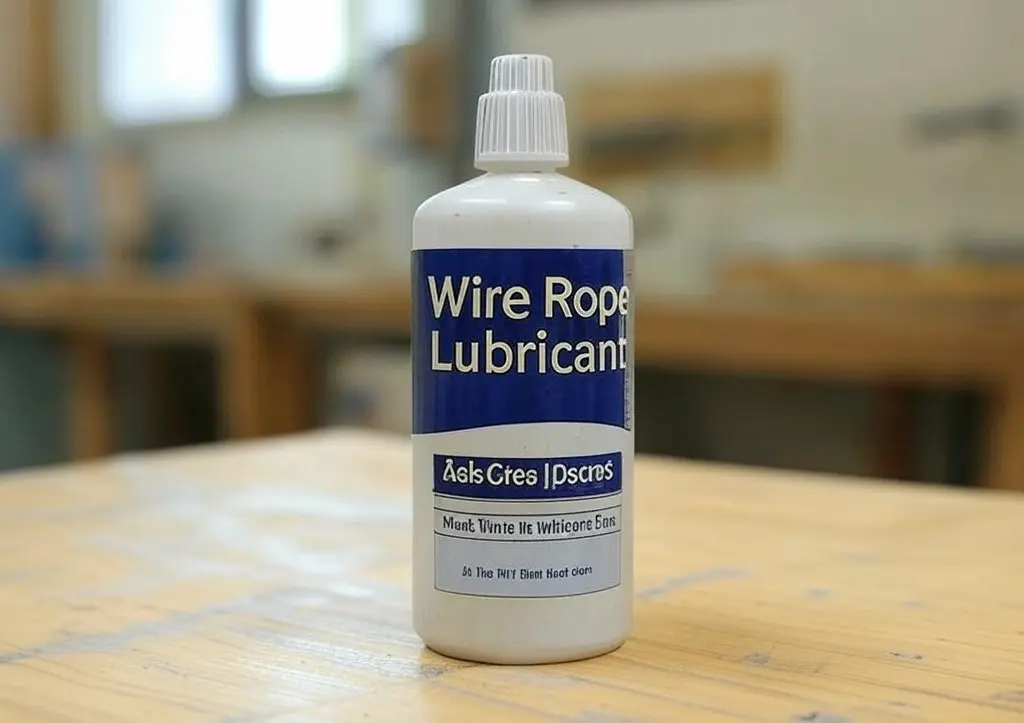
Lubricating a wire rope involves applying a liquid lubricant to reduce wear and friction while extending the rope’s lifespan. It’s an important element of maintaining the rope regularly.
The wire rope moves and bends, there is friction in the area where individual wires rub one and each other in the internal. This results in the sensation of heat, stiffness and small little pieces of wear as time passes. Lubricant covers the wires to stop this.
Friction can also occur externally as the rope passes through pulleys, sheaves, and around the drum’s ends. Lubricant helps reduce friction externally too.
The proper lubrication of wire rope enables it to move easily and flex without causing friction wear, or damage. This helps keep it safe and functional for longer.
Choosing the Right Lubricant
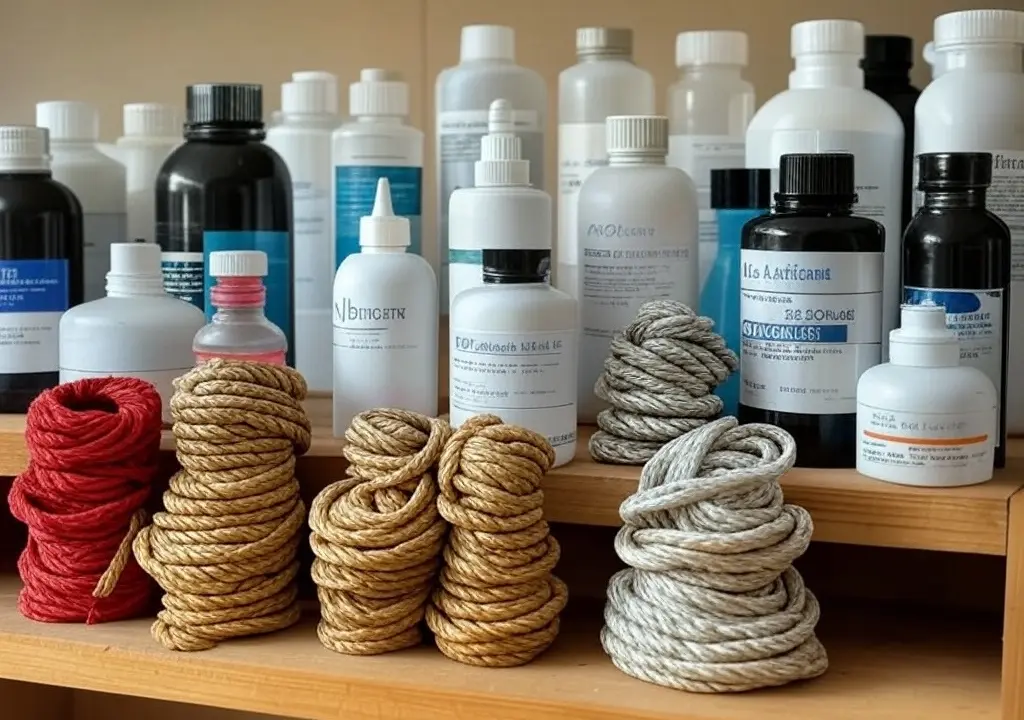
There are several main types of lubricants designed specifically for wire ropes.
- Lubricants made of oil such as gear or turbine oil.
- Grease grease lubricants such as calcium or petroleum greases.
- Dry lubricants such as molybdenum disulfide or molybdenum powder.
Lubricants based on oil provide good long-term penetration, but may be absorbed by the body. They are able to stick, but may not be able to penetrate the core. Dry lubricants do not attract dirt, but they must be applied frequently.
Think about factors such as the rope’s use and its environment to select the appropriate kind of lubricant to suit the application and environment. Making sure that the lubricant is compatible guarantees maximum protection of the rope.
How to Apply Wire Rope Lubricant
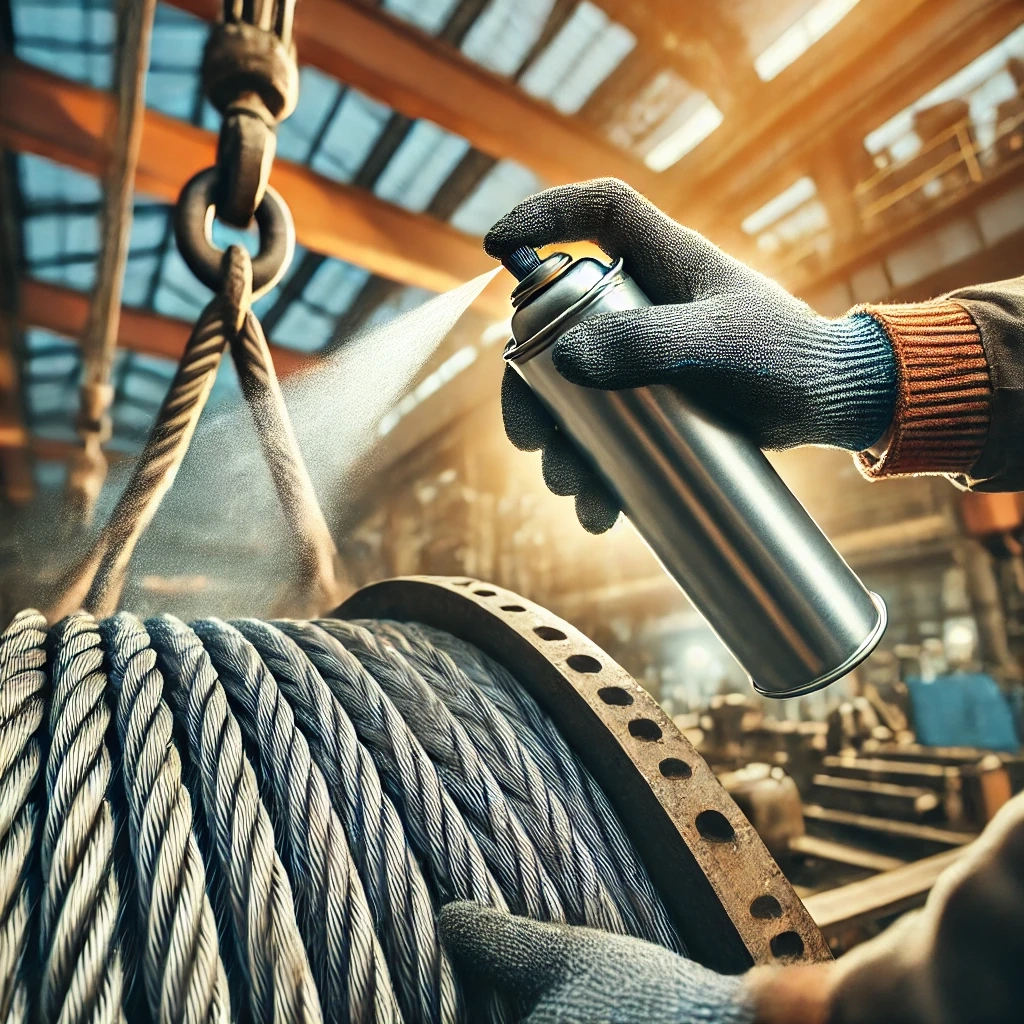
It is essential to apply the lubricant correctly to ensure that it is fully absorbed and covers the rope. Here are a few tips to apply it:
- The first step is to clean any grime, dirt or old lubricant off of the rope using soap or solvents. Dirt prevents penetration.
- Spray lubricant by brushing or dripping on the entire length while the rope is rotating. Get full coverage including inner strands.
- Apply enough lubricant to allow it to penetrate, but be careful not to cause excessive drips. Remove any excess runs.
- Make sure to lubricate the ropes more often when they are exposed to high temperatures, or exposed to the elements.
A proper application of lubrication to wire rope prolongs the life of the rope and helps avoid expensive downtime or costly replacements.
Warning Signs a Rope Needs Lubrication
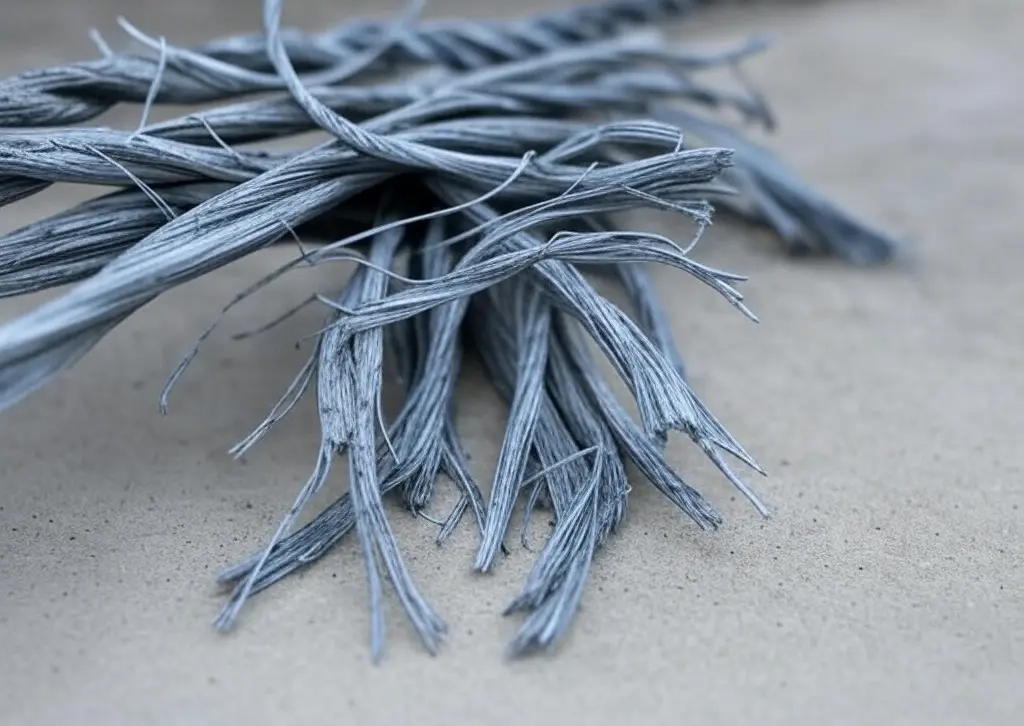
What are the signs to know when it’s the right time to oil the rope or wire? Watch out for these warning indicators:
- The visible wear, dirt or rust marks along the rope.
- The rope is stiff or rigid, which makes the rope difficult to move.
- The discoloration is caused by friction heat or scratching.
- Grinding, binding, or squeaking noises when it runs.
- Broken wires peeking out of the wires.
Each of these signs indicates an absence of oil lubrication. The prompt lubrication of these issues keeps the rope in good condition.
Storing Wire Rope Properly
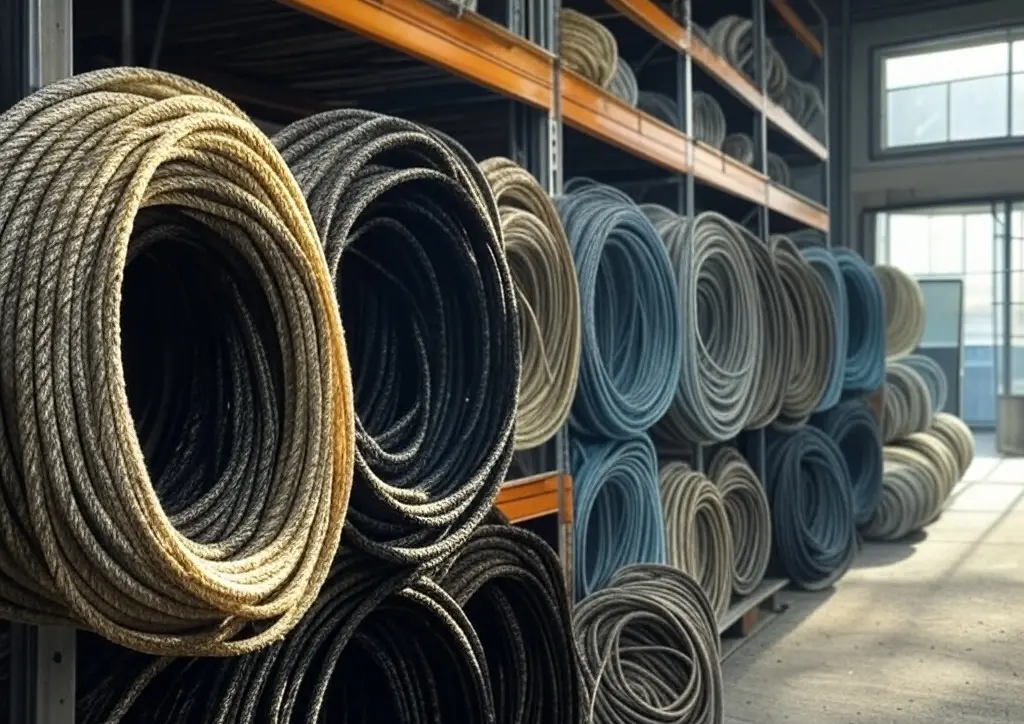
Storage that is properly maintained between uses is essential to ensure the health of wire rope. Use these storage guidelines:
- Hooks can be used to hang ropes vertically or racks to ensure they won’t sag or break.
- Do not let ropes touch the ground as it can attract dirt and water.
- Secure ropes from corrosive fumes and extreme weather.
- Rotate stock so that you start with older ropes before using newer ones.
Conclusion
A proper lubrication of wire ropes and storage ensures they run smoothly and safely to ensure a long-lasting service. The simple practice of maintaining will help in getting the most value from your wire rope resources.